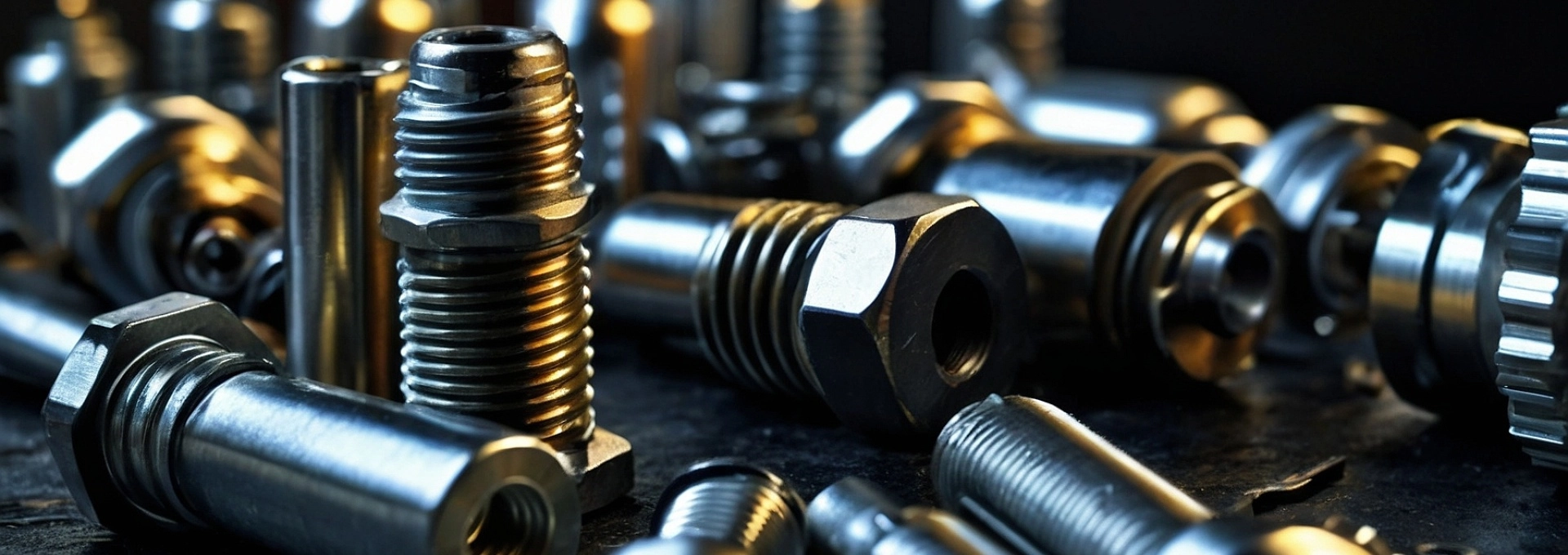
Les projets industriels requièrent une attention particulière quant au choix des fixations utilisées, car ces éléments jouent un rôle fondamental dans la sécurité et la performance des installations. Un expert en fixations apporte une valeur ajoutée considérable en optimisant la sélection, le dimensionnement et la mise en œuvre de ces composants critiques. Son expertise technique permet de garantir la fiabilité des assemblages dans des environnements souvent exigeants. En faisant appel à un spécialiste comme fabory.com, les industriels s'assurent de bénéficier des solutions les plus adaptées à leurs besoins spécifiques, tout en respectant les normes en vigueur. Cette approche sur-mesure contribue à améliorer la durabilité et la sécurité des installations, tout en maîtrisant les coûts sur le long terme.
Expertise technique pour des fixations industrielles optimales
L'expertise technique d'un spécialiste des fixations industrielles repose sur une connaissance approfondie des propriétés mécaniques et chimiques des matériaux, ainsi que sur la maîtrise des contraintes spécifiques aux différents secteurs d'activité. Cette compétence permet d'identifier avec précision les solutions les plus appropriées pour chaque application. L'expert prend en compte de nombreux paramètres tels que les charges statiques et dynamiques, les vibrations, la corrosion, les températures extrêmes ou encore les environnements chimiquement agressifs. Son analyse intègre également les aspects liés à la facilité de montage et de maintenance, ainsi que la durée de vie attendue des assemblages.
La sélection des fixations adaptées nécessite une compréhension fine des interactions entre les différents composants d'un système. L'expert évalue les conséquences potentielles d'une défaillance et recommande des solutions permettant de minimiser les risques. Il peut par exemple préconiser l'utilisation de fixations auto-freinantes pour prévenir le desserrage dans des conditions de vibrations importantes, ou encore suggérer des revêtements spécifiques pour améliorer la résistance à la corrosion. Cette approche globale contribue à optimiser la fiabilité et la longévité des installations industrielles.
L'expertise technique se traduit également par la capacité à effectuer des calculs complexes pour dimensionner correctement les assemblages. Ces calculs prennent en compte les efforts de traction, de cisaillement, de flexion et de torsion auxquels les fixations seront soumises. L'expert utilise des logiciels spécialisés et s'appuie sur des normes de calcul reconnues pour garantir la précision de ses recommandations. Cette rigueur dans le dimensionnement permet d'éviter les situations de sous-dimensionnement, sources potentielles de défaillances, mais aussi de sur-dimensionnement, qui engendreraient des surcoûts inutiles.
Types de fixations utilisées en milieu industriel
Les fixations industrielles se déclinent en une multitude de types, chacun présentant des caractéristiques spécifiques adaptées à différentes applications. La connaissance approfondie de cette diversité est essentielle pour sélectionner la solution optimale en fonction des contraintes techniques et économiques de chaque projet. Les experts en fixations maîtrisent les avantages et les limites de chaque type, permettant ainsi une utilisation judicieuse des différentes options disponibles.
Boulons et écrous pour assemblages solides
Les boulons et écrous constituent l'une des solutions de fixation les plus couramment utilisées dans l'industrie. Leur polyvalence et leur capacité à supporter des charges importantes en font des éléments incontournables pour de nombreux assemblages. Les boulons se déclinent en différentes classes de qualité, définies par leur résistance mécanique. Le choix de la classe de qualité dépend des contraintes spécifiques à l'application. Par exemple, les boulons de classe 8.8 sont couramment utilisés dans la construction mécanique générale, tandis que les classes 10.9 ou 12.9 sont privilégiées pour les applications nécessitant une résistance mécanique accrue.
La géométrie des boulons et écrous joue également un rôle crucial dans leur performance. Les experts peuvent recommander des designs spécifiques tels que des têtes hexagonales, des empreintes six pans creux ou des écrous auto-freinants en fonction des besoins de montage et de maintenance. Certaines applications nécessitent des boulons à tête fraisée pour obtenir une surface affleurante, tandis que d'autres requièrent des boulons à tête bombée pour des raisons de sécurité. La sélection du pas de filetage, fin ou gros, influence quant à elle la résistance à l'arrachement et la sensibilité au desserrage.
L'utilisation de boulons et écrous dans des environnements corrosifs nécessite une attention particulière au choix des matériaux et des revêtements. Les experts peuvent préconiser l'utilisation d'aciers inoxydables, de revêtements zinc-nickel ou de traitements de surface spécifiques pour garantir la durabilité des assemblages. Dans certains cas, l'emploi de boulons en matériaux composites peut être envisagé pour combiner légèreté et résistance à la corrosion. La maîtrise de ces différents aspects permet d'optimiser la durée de vie des assemblages boulonnés tout en minimisant les besoins de maintenance.
Rivets pour des liaisons permanentes résistantes
Les rivets offrent une solution de fixation permanente particulièrement adaptée aux assemblages soumis à des charges dynamiques importantes. Leur processus de mise en place, qui consiste à déformer plastiquement une partie du rivet, crée une liaison extrêmement solide et résistante aux vibrations. Les experts en fixations maîtrisent les différents types de rivets disponibles, tels que les rivets pleins, les rivets creux ou les rivets aveugles, et peuvent recommander la solution la plus appropriée en fonction des contraintes d'accessibilité et des charges à supporter.
Le choix du matériau du rivet est crucial pour assurer la compatibilité avec les matériaux assemblés et garantir la résistance à la corrosion. Les rivets en aluminium sont largement utilisés dans l'industrie aéronautique pour leur légèreté, tandis que les rivets en acier inoxydable sont privilégiés dans les environnements corrosifs. Les experts peuvent également recommander des rivets en matériaux spéciaux, comme le titane, pour des applications nécessitant une combinaison unique de propriétés mécaniques et de résistance à la corrosion. La géométrie du rivet, notamment la forme de la tête et la longueur du corps, est optimisée en fonction des épaisseurs à assembler et des contraintes mécaniques attendues.
L'utilisation de rivets nécessite une attention particulière à la préparation des surfaces et au dimensionnement des trous. Les experts en fixations peuvent fournir des recommandations précises sur les tolérances à respecter et les méthodes de perçage à utiliser pour garantir la qualité de l'assemblage. Ils peuvent également conseiller sur les équipements de pose les plus adaptés, qu'il s'agisse d'outils manuels, pneumatiques ou hydrauliques. Cette expertise permet d'optimiser le processus de rivetage, assurant ainsi une productivité élevée tout en maintenant un niveau de qualité constant.
Goujons filetés pour fixations démontables robustes
Les goujons filetés représentent une solution de fixation polyvalente, particulièrement appréciée dans les applications nécessitant un démontage fréquent ou une grande précision d'alignement. Ces éléments, constitués d'une tige filetée à ses deux extrémités, permettent de créer des assemblages robustes tout en facilitant les opérations de maintenance. Les experts en fixations peuvent recommander l'utilisation de goujons dans diverses situations, notamment pour l'assemblage de brides, la fixation de machines sur leurs socles ou encore la réalisation de liaisons mécaniques précises.
Le dimensionnement des goujons filetés requiert une analyse approfondie des charges axiales et radiales auxquelles ils seront soumis. Les experts prennent en compte non seulement les efforts statiques, mais également les sollicitations dynamiques et les éventuels phénomènes de fatigue. Le choix du matériau et du traitement de surface des goujons est crucial pour garantir leur résistance mécanique et leur tenue à la corrosion. Dans certains cas, l'utilisation de goujons en alliages spéciaux peut être préconisée pour répondre à des contraintes particulières, comme une résistance élevée aux hautes températures ou une compatibilité avec des environnements chimiques agressifs.
La mise en œuvre des goujons filetés nécessite une attention particulière à la qualité des taraudages et à la précision des ajustements. Les experts peuvent fournir des recommandations sur les couples de serrage à appliquer et sur l'utilisation éventuelle de produits de freinage pour prévenir le desserrage spontané. Dans certaines applications critiques, ils peuvent suggérer l'emploi de techniques de contrôle non destructif, comme le ressuage ou la magnétoscopie, pour vérifier l'intégrité des goujons après leur installation. Cette approche globale permet d'assurer la fiabilité et la durabilité des assemblages réalisés avec des goujons filetés.
Choix des matériaux adaptés aux conditions d'utilisation
La sélection des matériaux pour les fixations industrielles constitue une étape cruciale dans l'optimisation des assemblages. Cette décision impacte directement la résistance mécanique, la durabilité et la compatibilité des fixations avec leur environnement d'utilisation. Les experts en fixations disposent d'une connaissance approfondie des propriétés des différents matériaux disponibles, allant des aciers au carbone classiques aux alliages spéciaux en passant par les matériaux composites. Cette expertise leur permet de recommander la solution la plus adaptée en fonction des contraintes spécifiques de chaque application.
L'analyse des conditions d'utilisation inclut l'évaluation des contraintes mécaniques, thermiques et chimiques auxquelles les fixations seront soumises. Par exemple, dans un environnement marin, la résistance à la corrosion devient un critère prépondérant, orientant le choix vers des matériaux tels que les aciers inoxydables austénitiques ou les alliages de titane. Pour des applications à haute température, les experts peuvent préconiser l'utilisation d'alliages réfractaires capables de conserver leurs propriétés mécaniques dans des conditions extrêmes. Dans l'industrie chimique, la compatibilité des matériaux avec les produits manipulés guide la sélection vers des solutions résistantes aux attaques acides ou alcalines.
La prise en compte des phénomènes de fatigue et de fluage est également essentielle dans le choix des matériaux pour les fixations soumises à des sollicitations cycliques ou à des charges permanentes à haute température. Les experts peuvent recommander des nuances d'acier spécifiques ou des traitements thermiques adaptés pour améliorer la résistance à ces modes de défaillance. Dans certains cas, l'utilisation de matériaux composites peut être envisagée pour combiner légèreté et résistance mécanique, notamment dans les secteurs de l'aérospatiale ou des énergies renouvelables. Cette approche sur-mesure permet d'optimiser les performances des assemblages tout en maîtrisant les coûts sur l'ensemble du cycle de vie des installations, comme l'indique le tableau suivant :
Matériau | Résistance à la corrosion | Résistance mécanique | Coût relatif |
---|---|---|---|
Acier au carbone | Faible | Élevée | Bas |
Acier inoxydable 316 | Excellente | Moyenne | Élevé |
Titane | Excellente | Très élevée | Très élevé |
Dimensionnement précis des fixations par un expert
Le dimensionnement des fixations industrielles requiert une expertise approfondie pour garantir la sécurité et l'efficacité des assemblages. Cette étape cruciale nécessite la prise en compte de multiples facteurs tels que les charges statiques et dynamiques, les conditions environnementales et les exigences spécifiques de l'application. Un expert en fixations dispose des compétences et des outils nécessaires pour réaliser des calculs précis, assurant ainsi un dimensionnement optimal des éléments de fixation.
Calculs de résistance mécanique des assemblages
Les calculs de résistance mécanique constituent le cœur du processus de dimensionnement des fixations industrielles. Ces calculs prennent en compte les différents types de sollicitations auxquelles les assemblages seront soumis, notamment les efforts de traction, de cisaillement, de flexion et de torsion. Les experts utilisent des méthodes de calcul normalisées, telles que celles définies par les normes ISO ou ASME, pour déterminer les dimensions et les caractéristiques mécaniques requises pour les fixations. Ces calculs intègrent également des coefficients de sécurité adaptés à la criticité de l'application, garantissant ainsi une marge de sécurité appropriée.
L'analyse des contraintes au sein des assemblages boulonnés fait appel à des modèles mathématiques complexes, prenant en compte la répartition des efforts entre les différents éléments de fixation. Les experts peuvent utiliser des logiciels de simulation par éléments finis pour affiner leurs calculs, notamment dans le cas d'assemblages soumis à des charges non uniformes ou à des conditions de fonctionnement particulières. Cette approche permet d'optimiser le nombre et la disposition des fixations, assurant ainsi un équilibre entre performance mécanique et coût de l'assemblage.
La prise en compte des phénomènes de fatigue est particulièrement importante dans le dimensionnement des fixations soumises à des charges cycliques. Les experts analysent les courbes de fatigue des matériaux utilisés et appliquent des méthodes de cumul de dommages pour estimer la durée de vie des assemblages. Cette analyse permet de définir des intervalles de maintenance appropriés et de prévenir les défaillances par fatigue, contribuant ainsi à la fiabilité à long terme des installations industrielles.
Prise en compte des contraintes environnementales
Le dimensionnement des fixations industrielles ne se limite pas aux seules considérations mécaniques. Les contraintes environnementales jouent un rôle déterminant dans la durabilité et la fiabilité des assemblages. Les experts en fixations intègrent dans leurs calculs les effets de la température, de l'humidité, des agents chimiques et des rayonnements sur les propriétés des matériaux utilisés. Cette analyse approfondie permet de sélectionner les nuances et les traitements de surface les plus appropriés pour garantir la pérennité des installations dans leur environnement spécifique.
Les variations de température constituent l'un des principaux défis à relever lors du dimensionnement des fixations. Les dilatations et contractions thermiques différentielles entre les éléments assemblés peuvent générer des contraintes supplémentaires sur les fixations. Les experts utilisent des modèles thermomécanique pour évaluer ces effets et déterminer les jeux et les tolérances nécessaires pour accommoder ces variations dimensionnelles. Dans certains cas, l'utilisation de rondelles élastiques ou de systèmes de compensation thermique peut être préconisée pour maintenir la tension des assemblages boulonnés sur une large plage de températures.
La corrosion représente une autre problématique majeure à prendre en compte dans le dimensionnement des fixations. Les experts évaluent le potentiel corrosif de l'environnement et ses effets sur la durée de vie des assemblages. Cette analyse peut conduire à la recommandation de matériaux résistants à la corrosion, tels que les aciers inoxydables ou les alliages de titane, ou à la préconisation de traitements de surface spécifiques comme la galvanisation à chaud ou les revêtements céramiques. Dans certains cas, l'utilisation de systèmes de protection cathodique peut être envisagée pour prolonger la durée de vie des fixations dans des environnements particulièrement agressifs.
Les contraintes liées aux vibrations et aux chocs nécessitent également une attention particulière lors du dimensionnement des fixations. Les experts analysent les spectres de vibration auxquels les assemblages seront soumis et évaluent les risques de desserrage ou de rupture par fatigue. Cette analyse peut conduire à la recommandation de solutions spécifiques telles que l'utilisation d'écrous autobloquants, de rondelles élastiques ou de systèmes de freinage chimique. Dans certains cas, des essais de vibration peuvent être réalisés pour valider la tenue des assemblages dans des conditions représentatives de leur utilisation réelle.
Optimisation des coûts grâce au sur-mesure
L'optimisation des coûts constitue un aspect fondamental du dimensionnement des fixations industrielles. Les experts en fixations s'efforcent de trouver le meilleur compromis entre performance technique et viabilité économique. Cette approche sur-mesure permet de minimiser les coûts directs liés à l'achat des fixations, mais également les coûts indirects associés à leur installation, leur maintenance et leur remplacement éventuel. L'analyse du coût global sur le cycle de vie des assemblages guide les choix techniques et permet de justifier l'utilisation de solutions plus onéreuses à l'achat mais plus économiques sur le long terme.
La standardisation des fixations au sein d'un projet ou d'une entreprise constitue un levier d'optimisation des coûts. Les experts peuvent recommander l'utilisation d'un nombre limité de références de fixations, répondant à la majorité des besoins identifiés. Cette approche permet de réduire les coûts logistiques, de simplifier la gestion des stocks et de bénéficier d'économies d'échelle lors des approvisionnements. La création d'un catalogue de fixations standardisées, adapté aux besoins spécifiques de l'entreprise, facilite également la conception des assemblages et réduit les risques d'erreurs lors de la spécification ou de l'installation des fixations.
L'optimisation de la quantité de fixations utilisées dans un assemblage représente un autre axe d'amélioration des coûts. Les experts en fixations utilisent des méthodes de calcul avancées, telles que l'analyse par éléments finis, pour déterminer le nombre minimal de fixations nécessaire pour garantir la tenue mécanique de l'assemblage. Cette approche permet de réduire non seulement le coût des fixations elles-mêmes, mais également le temps de montage et les risques associés à un surdimensionnement des assemblages. Dans certains cas, la modification de la conception des pièces à assembler peut permettre de réduire significativement le nombre de fixations requises, générant ainsi des économies substantielles.
La prise en compte des contraintes de montage et de maintenance dès la phase de dimensionnement des fixations contribue également à l'optimisation des coûts. Les experts peuvent recommander l'utilisation de fixations à mise en place rapide, telles que des systèmes de fixation quart de tour ou des rivets aveugles, pour réduire les temps d'assemblage. De même, le choix de fixations facilitant les opérations de maintenance, comme des boulons à tête imperdable ou des écrous captifs, peut générer des économies significatives sur la durée de vie des installations. Cette approche globale du dimensionnement des fixations permet d'optimiser non seulement les coûts d'acquisition, mais également les coûts opérationnels sur l'ensemble du cycle de vie des équipements industriels.
Conformité aux normes de sécurité en vigueur
La conformité aux normes de sécurité constitue un aspect incontournable du dimensionnement des fixations industrielles. Les experts en fixations maîtrisent les réglementations nationales et internationales applicables aux différents secteurs d'activité, assurant ainsi la légalité et la sécurité des installations. Cette connaissance approfondie des normes permet non seulement de garantir la conformité des assemblages, mais également d'optimiser leur conception en exploitant pleinement les possibilités offertes par les cadres réglementaires.
Les normes ISO (Organisation internationale de normalisation) jouent un rôle prépondérant dans la standardisation des fixations industrielles à l'échelle mondiale. Par exemple, la norme ISO 898-1 définit les caractéristiques mécaniques des éléments de fixation en acier au carbone et en acier allié. Cette norme établit un système de classification des boulons, vis et goujons en fonction de leur résistance mécanique, facilitant ainsi leur spécification et leur utilisation dans divers contextes industriels. Les experts s'appuient sur ces normes pour sélectionner les fixations appropriées en fonction des charges et des conditions d'utilisation prévues.
Dans le domaine de la construction métallique, l'Eurocode 3 (EN 1993) fournit des règles de calcul pour le dimensionnement des structures en acier, incluant les assemblages boulonnés. Cette norme européenne définit les méthodes de calcul de la résistance des boulons soumis à diverses sollicitations, telles que la traction, le cisaillement ou leur combinaison. Les experts en fixations utilisent ces méthodes pour dimensionner les assemblages conformément aux exigences de sécurité en vigueur, tout en optimisant la quantité de matière utilisée.
La directive européenne 2006/42/CE, relative aux machines, impose des exigences strictes en matière de sécurité pour les équipements industriels. Cette directive aborde notamment la question des fixations utilisées dans les assemblages critiques pour la sécurité. Les experts veillent à ce que les fixations sélectionnées répondent aux exigences de cette directive, en termes de résistance mécanique, de durabilité et de fiabilité. Ils s'assurent également que la documentation technique fournie avec les fixations est conforme aux exigences de traçabilité et d'information imposées par la directive. Le tableau suivant vous donne un aperçu :
Norme | Domaine d'application | Principaux aspects couverts |
---|---|---|
ISO 898-1 | Fixations métalliques | Caractéristiques mécaniques des éléments de fixation en acier |
EN 1993 (Eurocode 3) | Construction métallique | Calcul des assemblages boulonnés dans les structures en acier |
Directive 2006/42/CE | Machines industrielles | Exigences de sécurité pour les fixations dans les équipements industriels |
Les normes spécifiques à certains secteurs industriels, tels que l'aéronautique, l'automobile ou le nucléaire, imposent des exigences supplémentaires en matière de fixations. Par exemple, la norme AS9100 pour l'industrie aérospatiale définit des critères stricts pour la qualification des fournisseurs de fixations et la traçabilité des produits. Les experts en fixations maîtrisent ces normes sectorielles et peuvent recommander des solutions conformes aux exigences spécifiques de chaque industrie, garantissant ainsi la sécurité et la fiabilité des assemblages dans des applications critiques.